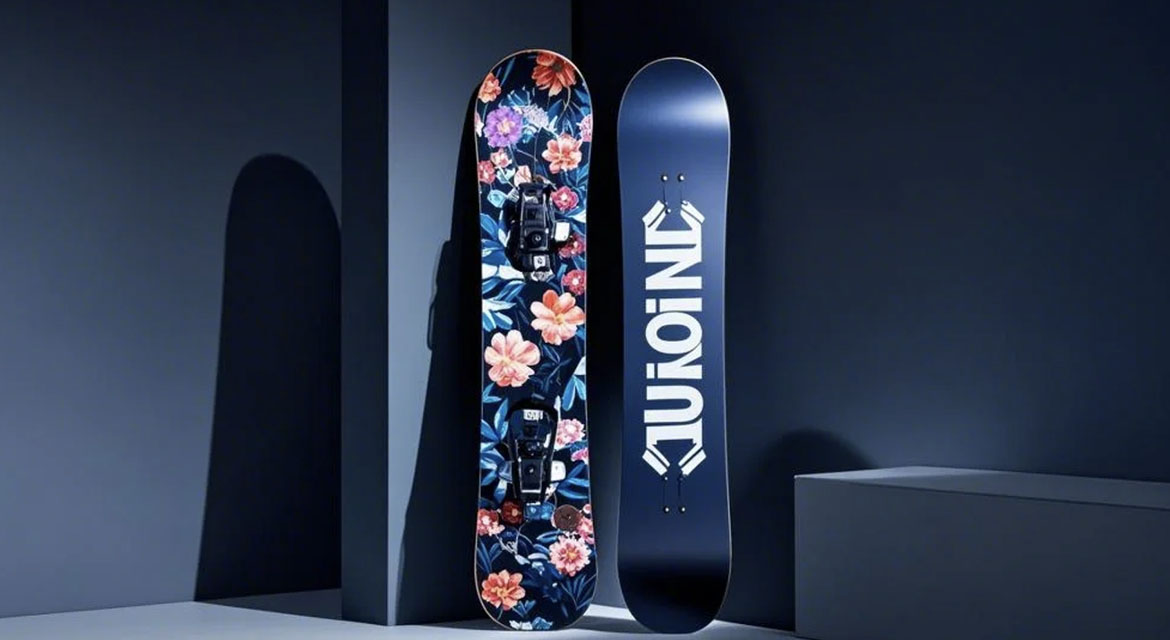
Snowboards

Type
All-Mountain, Freestyle, Powder

Material
Maple, Poplar, Bamboo, Or Paulownia

Printing
Sublimation, Screen Printing, Digital Direct Printing, Etc.

ECO
ASTM F963 ,CPSC
- 1. Design and Prototyping
- Concept Development: Determine the snowboard type (e.g., all-mountain, freestyle, powder), shape (camber, rocker, hybrid), flex pattern.
- Digital Modeling: Use CAD software to design the board’s profile, sidecut, and core structure.
- Prototyping: Create physical prototypes to test flex, torsion, and performance in real-world conditions.
2. Material Selection- Core Materials:
- Wood: Lightweight and strong woods like maple, poplar, bamboo, or paulownia (often laminated for optimal flex and durability).
- Composite/Foam: Carbon fiber, fiberglass, or honeycomb cores for high-performance boards.
- Base Material: Ultra-high-molecular-weight polyethylene (UHMW-PE), either sintered (durable, high-speed) or extruded (low-maintenance).
- Top Sheet: Fiberglass, nylon, or ABS plastic with graphics.
- Edges: Steel edges for grip and durability.
- Laminates: Fiberglass or carbon fiber layers for stiffness and response.
- Adhesives: Epoxy resins to bond layers.
3. Core Preparation- Wood Core Construction:
- Wood strips are cut, laminated, and shaped to match the board’s profile.
- Channels or holes are added to reduce weight (e.g., “corking”).
- Composite Core Molding: Foam or carbon cores are CNC-machined to precise dimensions.
4. Layup Process- Layer Stacking:
- Base Layer: UHMW-PE base is placed on the mold.
- Steel Edges: Pre-bent steel edges are positioned along the base’s perimeter.
- Core Placement: The wood or composite core is centered on the base.
- Fiberglass/Carbon Layers: Fiberglass sheets (woven or unidirectional) are layered above and below the core.
- Top Sheet: The decorative top layer is added.
- Adhesive Application: Epoxy resin is applied between layers to ensure bonding.
5. Pressing- Mold Setup: The layered “sandwich” is placed into a hydraulic press with a heated mold.
- Heat and Pressure:
- Temperature: ~150–180°C (300–350°F) to activate the epoxy.
- Pressure: ~300–500 psi to compress layers and shape the board’s camber/rocker profile.
- Curing: The board remains in the press for 15–30 minutes to harden.
6. Trimming and Shaping- CNC Machining: Excess material is trimmed from the edges.
- Sidecut Profiling: The board’s sidecut (hourglass shape) is precision-cut.
- Edge Tuning: Steel edges are ground to a sharp 90° angle for ice grip.
7. Sidewall and Edge Finishing- Sidewall Installation: ABS or urethane sidewalls are added to protect the core (optional for “cap” construction boards).
- Edge Detailing: Edges are polished, deburred, and waxed to prevent rust.
8. Surface Finishing- Sanding: The board is sanded smooth for a uniform finish.
- Graphics: Designs are applied via sublimation (dye infused into the top sheet) or screen printing.
- Clear Coat: A protective UV-resistant coating is applied.
9. Drilling and Binding Mounting- Insert Installation: Threaded metal inserts are embedded into the board for binding attachment.
- Drilling: Holes are precision-drilled to match industry-standard binding patterns (e.g., 4×4, Channel System).
10. Quality Control- Flex and Torsion Testing: Boards are flexed manually or mechanically to ensure consistency.
- Edge Integrity: Edges are checked for sharpness and alignment.
- Base Inspection: The base is polished and checked for scratches or air bubbles.
- Weight and Balance: Boards are weighed and balanced to meet specifications.
11. Packaging and Distribution- Waxing: A factory wax is applied to protect the base.
- Labeling: Includes size, flex rating, and safety certifications (e.g., ISO 6001).
- Packaging: Boards are wrapped in protective film, boxed, and shipped to retailers.
Key Considerations- Performance: Balancing flex, torsional stiffness, and weight for specific riding styles.
- Durability: Ensuring resistance to impact, moisture, and temperature extremes.
- Sustainability: Use of FSC-certified wood, bio-resins, or recycled materials.
- Customization: Brands often offer personalized graphics or core configurations.
Variations- Handcrafted Boards: Smaller brands use artisanal techniques for unique shapes/materials.
- Splitboards: Designed for backcountry use, these feature a separable core for climbing.
- Eco-Friendly Models: Bamboo cores, plant-based resins, and recycled bases.