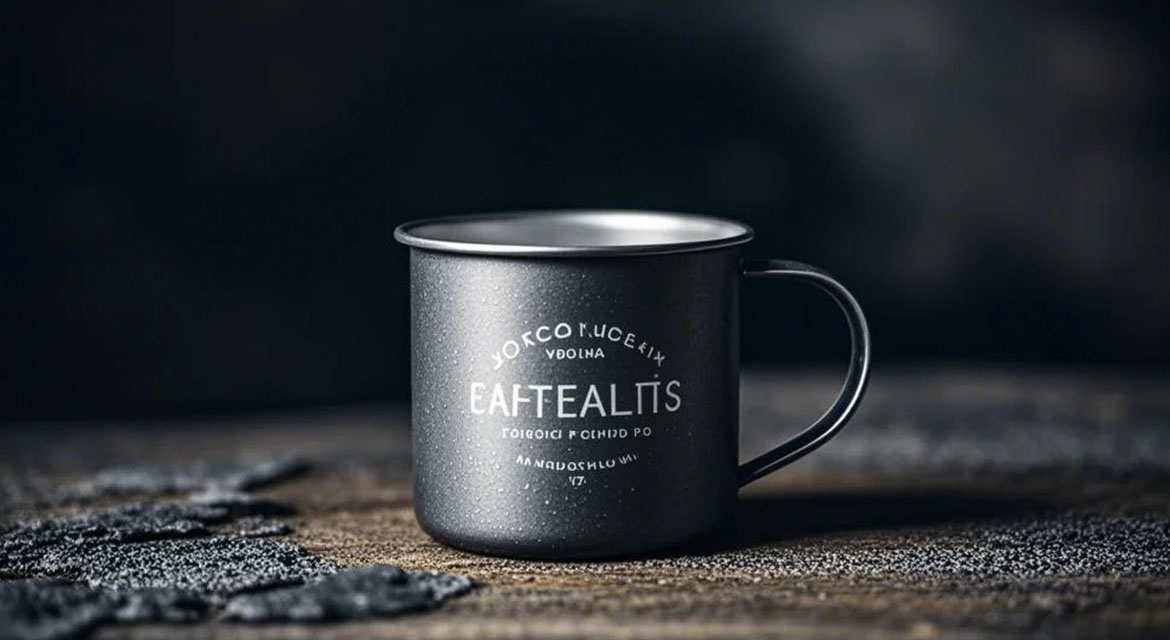
Enamel Mug

Material
Low-Carbon Steel Sheets, Glass Mixture

Surface
Degreasing, Pickling, Neutralization

Decoration
Screen Printing, Decals, Hand-Painting.

ECO
Steel Is Recyclable
- Material Selection:
- Carbon Steel Sheets: High-quality, low-carbon steel sheets are selected for their durability and formability.
- Enamel Frit: A powdered glass mixture (silica, feldspar, borax) with metal oxides for color and adhesion.
- Blanking and Cutting:
- Steel sheets are cut into circular blanks using hydraulic presses or laser cutting machines.
- Stamping/Pressing:
- Blanks are pressed into mug shapes using deep-drawing dies.
- Handle Formation:
- Integrated handles: Stamped as part of the mug body.
- Separate handles: Cut, shaped, and welded/riveted to the mug body pre-enameling.
- Surface Preparation:
- Degreasing: Remove oils and contaminants via alkaline baths.
- Pickling: Immersion in acid (e.g., sulfuric or hydrochloric) to eliminate rust and scale.
- Neutralization: Rinsed to remove acid residues.
- Base Enamel Application:
- Wet Process: Mug is dipped or sprayed with a slurry of enamel frit and water.
- Dry Process: Electrostatic powder coating for even distribution.
- Firing:
- Mugs are fired in a kiln at 800–900°C to melt and fuse the enamel into a smooth, glassy layer.
- Double Firing: Some processes apply a second enamel coat for durability.
- Decoration:
- Screen Printing: Designs are applied using heat-resistant pigments through mesh stencils.
- Decals: Pre-printed designs transferred onto the mug and fired to bond with the enamel.
- Hand-Painting: Artisan techniques for custom designs (rare in mass production).
- Final Firing:
- Decorated mugs are fired again at 700–800°C to set the colors and ensure adhesion.
- Edge Finishing:
- The rim is rolled or ground to eliminate sharp edges.
- Optional silicone or rubber grip added to the handle base.
- Quality Control:
- Visual Inspection: Check for bubbles, cracks, or uneven coatings.
- Adhesion Test: Tap test to detect delamination.
- Leak Test: Ensure structural integrity (for lidded mugs).
- Packaging:
- Mugs are wrapped in protective materials (bubble wrap, cardboard sleeves).
- Bulk packaging for wholesale or retail display.
- Durability: Enamel thickness (~0.1–0.3 mm) balances chip resistance and flexibility.
- Sustainability: Steel is recyclable, though enamel coating complicates the process.
- Safety: Lead-free pigments and proper ventilation during firing.
- Campfire Mugs: Thicker enamel for heat resistance.
- Vintage Styles: Distressed finishes achieved through controlled oxidation.
- Material Selection: