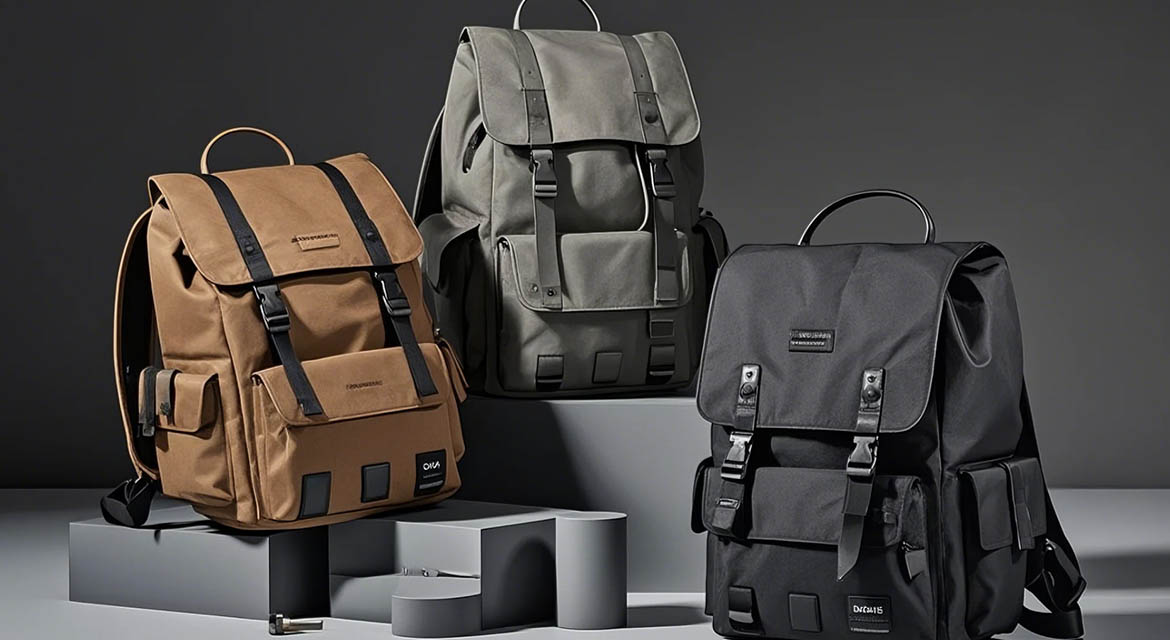
Backpacks

Type
Hiking, School, Travel

Material
Nylon, Polyester, Or Canvas. Waterproof Coatings PU, TPU

Printing
Screen Printing, Thermal Transfer, Digital Direct Printing, Etc.

ECO
Organic Cotton, Recycled Polyester, Etc
- 1. Design and Prototyping
- Concept Development: Determine the backpack’s purpose (e.g., hiking, school, travel), capacity, and target audience.
- Technical Design:
- Create sketches or CAD models to define dimensions, compartments, straps, and ergonomics.
- Select features like padded laptop sleeves, hydration systems, or MOLLE webbing.
- Prototyping: Sew a sample using mock-up materials to test fit, comfort, and functionality.
2. Material Selection- Fabrics:
- Shell: Durable materials like nylon, polyester, or canvas. Waterproof coatings (e.g., PU, TPU) may be added.
- Lining: Lightweight polyester or recycled fabrics for interior compartments.
- Padding: EVA foam or mesh for straps and back panels.
- Hardware: Zippers (YKK® is common), buckles, D-rings, and sliders (metal or plastic).
- Thread and Reinforcements: High-strength polyester thread; bar tacks or webbing for stress points.
3. Pattern Making and Cutting- Pattern Creation: Convert designs into 2D templates for each panel (body, straps, pockets).
- Fabric Cutting:
- Automated CNC cutting machines or laser cutters ensure precision.
- Layers of fabric are cut to minimize waste.
4. Component Manufacturing- Strap Production:
- Cut webbing or foam-padded straps; stitch adjusters and buckles.
- Zipper Assembly: Attach zipper tapes to fabric panels.
- Molded Parts: Injection-molded plastic or metal components (e.g., buckles, loops).
5. Sewing and Assembly- Panel Stitching: Sew outer shell panels, pockets, and dividers.
- Lining Attachment: Add interior compartments and lining.
- Hardware Integration: Attach zippers, straps, and buckles.
- Reinforcement: Double-stitch stress points (shoulder straps, bottom panels).
- Padding Installation: Sew foam into back panels and shoulder straps.
6. Surface Finishing- Printing/Embroidery: Apply logos, patterns, or reflective strips via screen printing, heat transfer, or embroidery.
- Waterproofing: Seal seams with waterproof tape or coatings.
- Edge Binding: Finish raw edges with bias tape or laser cutting to prevent fraying.
7. Quality Control- Durability Testing:
- Load testing (e.g., 20–30 kg weights) to check strap strength.
- Zipper cycle tests (opening/closing 1,000+ times).
- Inspection: Check stitching consistency, alignment, and hardware function.
- Safety Compliance: Meet regulations for flammability, chemical safety (e.g., REACH, CPSIA).
8. Packaging and Distribution- Folding/Packing: Compress backpacks for efficient shipping; some include cardboard inserts to retain shape.
- Labeling: Attach care instructions, branding, and certifications (e.g., OEKO-TEX®, recycled content).
- Shipping: Distribute to retailers or direct-to-consumer via bulk cartons.
Key Considerations- Ergonomics: Adjustable straps, ventilated back panels, and weight distribution for comfort.
- Durability: Reinforced stitching, abrasion-resistant fabrics, and corrosion-resistant hardware.
- Sustainability: Use of recycled polyester, organic cotton, or PFC-free water repellents.
- Customization: Options for personalized colors, patches, or modular attachments.
Variations in Production- Technical Backpacks (e.g., hiking, military): Include advanced features like load-bearing frames, hydration bladders, and weatherproof materials.
- Urban/Fashion Backpacks: Focus on aesthetics, minimalist designs, and premium materials (e.g., leather).
- Eco-Friendly Models: Made with upcycled fabrics, plant-based dyes, or biodegradable components.