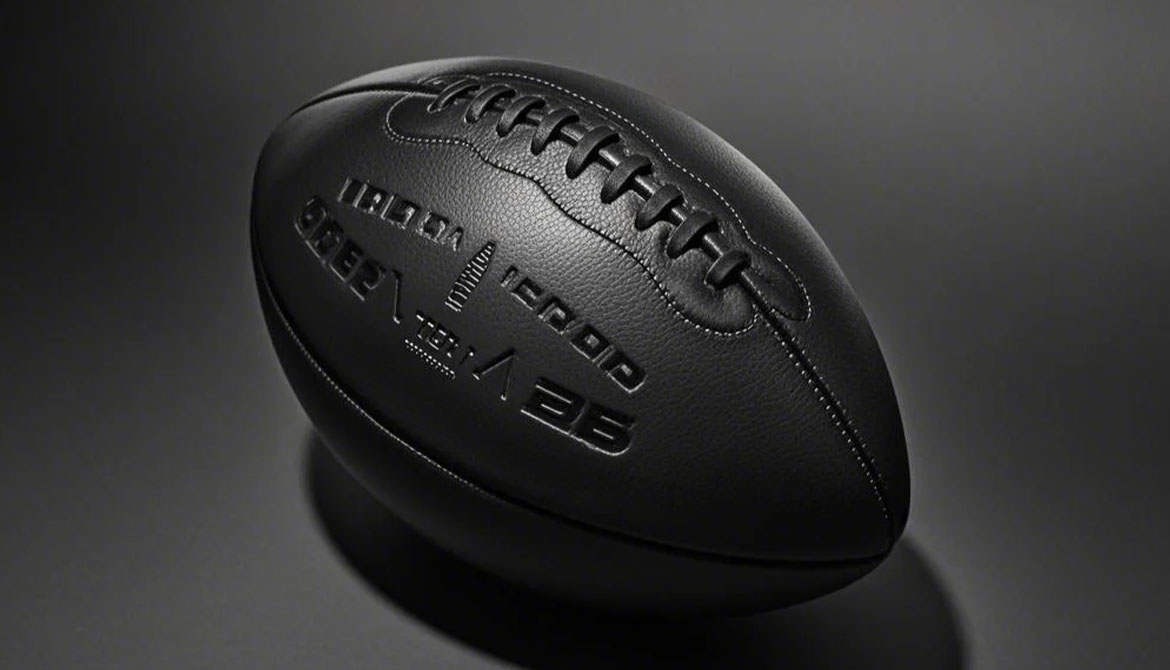
Rugby Ball

Type
Training Balls, Match Balls

Material
Leather, Polyurethane, PVC, Thermoplastic Polyurethane

Printing
Screen Printing, Digital Direct Printing, Etc.

Regulatory
28–30 cm Long, 58–62 cm Circumference, 410–460 grams.
1. Design & Material Selection
Regulatory Compliance: Follows World Rugby specifications for size (size 5 for adults: 28–30 cm long, 58–62 cm circumference) and weight (410–460 grams).
Outer Casing:
Traditional: Leather (treated for water resistance) for premium match balls.
Modern: Synthetic materials (polyurethane, PVC, or thermoplastic polyurethane) for durability, all-weather grip, and cost efficiency.
Bladder: Latex or butyl rubber for air retention and pressure consistency.
Lining: Layers of polyester or cotton fabric between the casing and bladder to maintain shape.
2. Panel Cutting
Four-Panel Design: Die-cut synthetic or leather sheets into four identical oval panels.
Surface Texture: Embossed or molded with pebbling/chevron patterns to enhance grip.
Reinforcements: Edges are reinforced with adhesive or fabric strips for durability.
3. Bladder Production
Latex/Butyl Molding: Bladders are molded into a rugby ball shape and cured.
Valve Installation: A one-way air valve is inserted for inflation.
4. Panel Assembly
Lining Application: Fabric layers are glued or laminated to the inner side of each panel.
Panel Stitching/Bonding:
Hand-Stitching (Premium Balls): Panels are sewn together with waxed polyester thread, creating raised seams for better grip.
Thermal Bonding (Recreational Balls): Panels are fused using heat and adhesive for seamless construction.
Bladder Insertion: The bladder is placed inside the stitched casing.
5. Inflation & Shaping
Pre-Inflation: The ball is partially inflated to stretch the casing and align panels.
Final Shaping: Inflated to regulation pressure (9.5–10 psi) and heat-treated to set the shape.
6. Quality Control
Pressure Test: Check for air leakage over 24–48 hours.
Weight & Size: Verify compliance with World Rugby standards.
Durability Testing: Simulate kicks, passes, and scrums to test seam strength and wear resistance.
Aerodynamics: Wind tunnel testing for flight stability.
7. Branding & Finishing
Printing: Logos, certifications, and design elements are screen-printed or heat-transferred.
Surface Treatment: Apply coatings for UV/water resistance or enhanced grip.
8. Packaging
Deflated, folded, and boxed with care instructions.
Match balls may include a pump and carry bag.