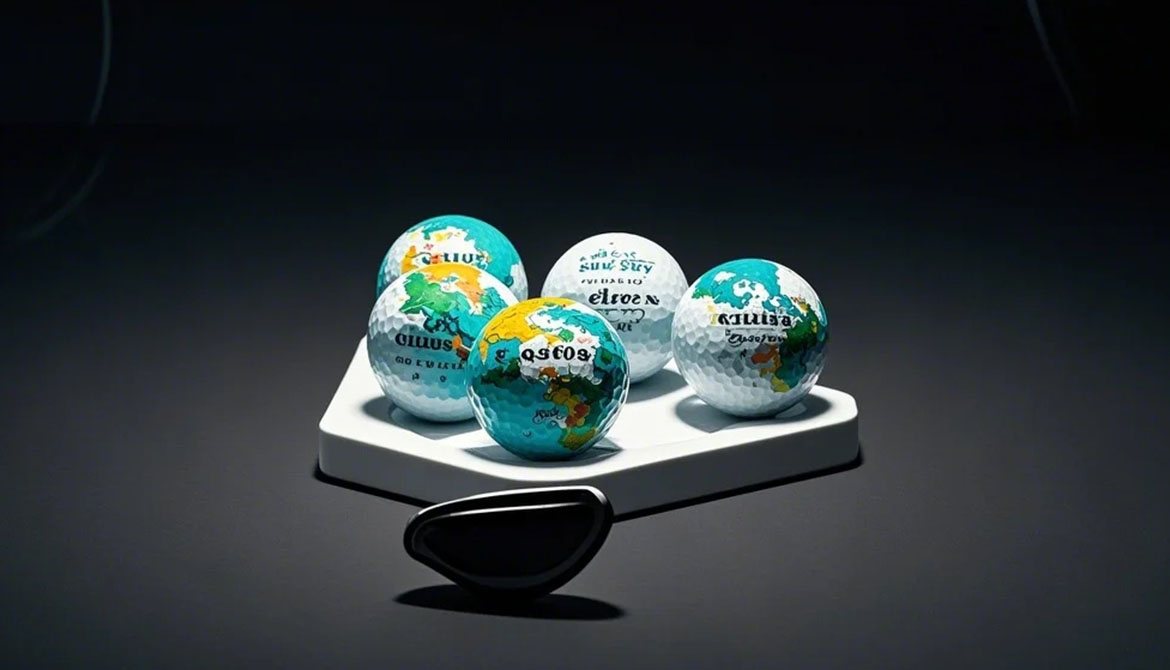
Golf Ball

Material
Synthetic Rubber,

Dimple Design
Hexagonal, Tetrahedral

Painting
Colored Paint, Pad-Printed Or Stamped

Regulatory
Conforms to USGA/R&A
- 1. Design & Material Selection
- Core Design:
- Solid Core: Typically made of synthetic rubber (e.g., polybutadiene) blended with additives like zinc oxide for energy transfer.
- Layer Construction:
- Two-Piece: Core + durable ionomer cover (e.g., Surlyn®) for distance and durability.
- Multi-Layer (3–5+ pieces): Adds mantle layers (ionomer, thermoplastic) to optimize spin and control.
- Cover Material:
- Urethane: Premium balls for soft feel and high spin.
- Surlyn®: Durable, cut-resistant for recreational use.
2. Core Production
- Mixing: Rubber compounds are blended with curing agents and accelerators.
- Compression Molding:
- The mixture is heated and pressed into spherical cores under high pressure.
- Cores are cooled and polished to ensure smoothness.
3. Layer Application
- Mantle Layers (for multi-layer balls):
- Thermoplastic or ionomer materials are injection-molded around the core.
- Enhances energy transfer and reduces spin for longer drives.
- Intermediate Layers: Optional additional layers for spin control or feel.
4. Cover Molding
- Injection Molding:
- Urethane or Surlyn® is injected into dimpled molds around the layered core.
- The mold’s cavity defines the ball’s dimple pattern (300–500 dimples).
- Cooling: Rapid cooling solidifies the cover while retaining dimple geometry.
5. Dimple Design & Aerodynamics
- Dimple Patterns: Proprietary designs (e.g., hexagonal, tetrahedral) optimize lift and reduce drag.
- Testing: Wind tunnel and robotic swing tests validate flight stability and distance.
6. Painting & Branding
- Base Coat: White or colored paint is applied via automated spray systems.
- Printing: Logos, numbers, and alignment aids are pad-printed or stamped.
- Clear Coat: A UV-resistant layer protects the finish.
7. Quality Control
- Weight & Size: Must meet USGA/R&A standards (≤ 1.620 oz, 1.68” diameter).
- Roundness: Checked via laser scanners; deviations > 0.01” are rejected.
- Compression: Tested to ensure consistency (e.g., 70–100 compression ratings).
- Performance: Robot-tested for launch angle, spin rate, and carry distance.
8. Packaging
- Balls are sorted into sleeves (3) or boxes (12) with branding and performance details.
- Recyclable or eco-friendly packaging is increasingly used.
- Core Design: