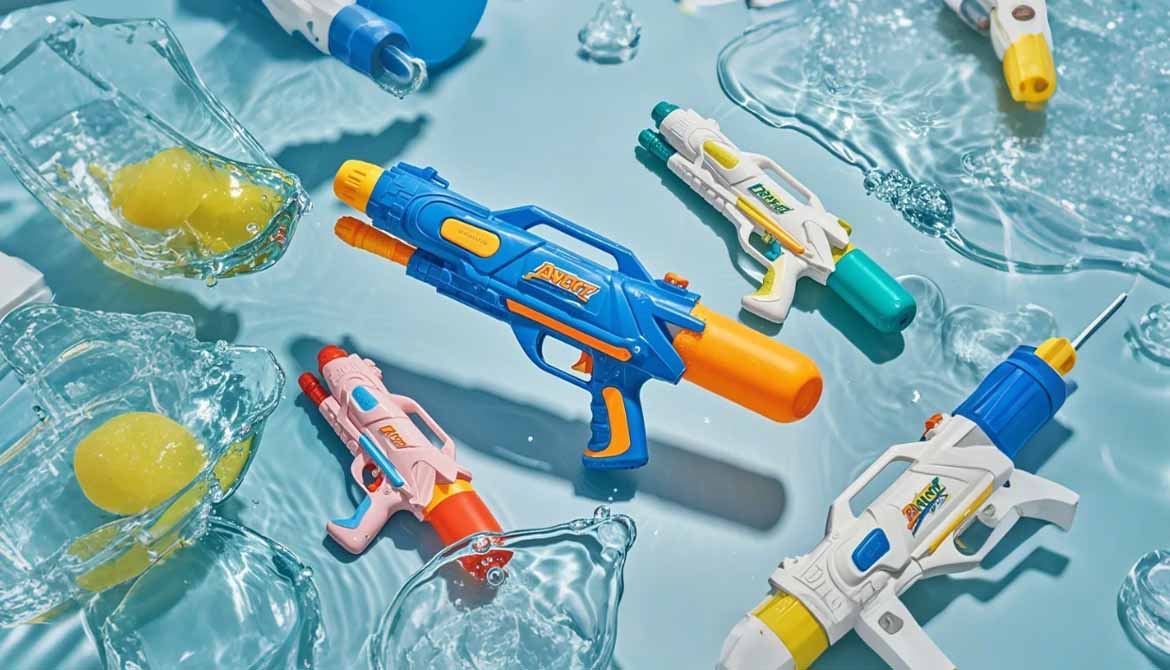
Water Pistol

Material
ABS, Polypropylene

Mold
Body, Trigger, Pump, Nozzle

Customization
Color Variants Or Themed

ECO
Recycled Plastics, ASTM F963, EN71
- Design & Prototyping
- Concept Development: Create initial sketches focusing on ergonomics, aesthetics, and functionality (e.g., grip design, water capacity).
- 3D Modeling: Use CAD software to refine dimensions, internal mechanisms (pump, nozzle), and assembly structure.
- Prototyping: 3D-print or mold a prototype to test water pressure, trigger responsiveness, and leak resistance.
- Material Selection
- Plastic Components:
- Body/Reservoir: ABS or polypropylene for durability and lightweight properties.
- Seals/O-rings: Silicone or rubber to prevent leaks.
- Mechanical Parts:
- Springs: Stainless steel for pump mechanism.
- Nozzle: Precision-molded plastic for controlled water flow.
- Safety Compliance: Non-toxic, BPA-free materials; smooth edges to meet toy safety standards (e.g., ASTM F963, EN71).
- Plastic Components:
- Mold Creation
- Injection Molds: CNC-machined aluminum or steel molds for each component (body, trigger, pump, nozzle).
- Quality Assurance: Molds are tested to ensure dimensional accuracy and seamless part assembly.
- Injection Molding
- Plastic Pellet Melting: Granules of ABS/polypropylene are heated to a molten state.
- Molding Process: Molten plastic is injected into molds under high pressure.
- Cooling & Ejection: Parts cool, solidify, and are ejected for post-processing (trimming excess flash).
- Component Manufacturing
- Pump Assembly:
- Piston, cylinder, and spring are assembled to create the pressurization mechanism.
- Nozzle Production: Molded to specific bore sizes for desired spray patterns (stream, mist).
- Trigger Mechanism: Molded with interlocking gears or levers to activate the pump.
- Pump Assembly:
- Assembly Line Process
- Automatic/Manual Assembly:
- Reservoir Attachment: Secured to the body.
- Pump Integration: Connected to the trigger and nozzle.
- Seal Installation: O-rings placed at joints to prevent leaks.
- Ultrasonic Welding/Screws: Parts fused or fastened for durability.
- Decorative Finishing: Painting, decals, or pad printing for colors/logos.
- Automatic/Manual Assembly:
- Quality Control & Testing
- Leak Testing: Submerged or pressurized to check for water seepage.
- Functionality Tests:
- Trigger pull force measurement.
- Spray distance/consistency evaluation (e.g., 10–30 ft range).
- Safety Checks: Compliance with international standards (sharp edges, choking hazards).
- Packaging & Labeling
- Blister Packs/Boxes: Secure packaging with clear display windows.
- Labels: Age recommendations, safety warnings, and instructions for use.
- Barcodes & Certifications: CE, ASTM, or ISO marks for retail compliance.