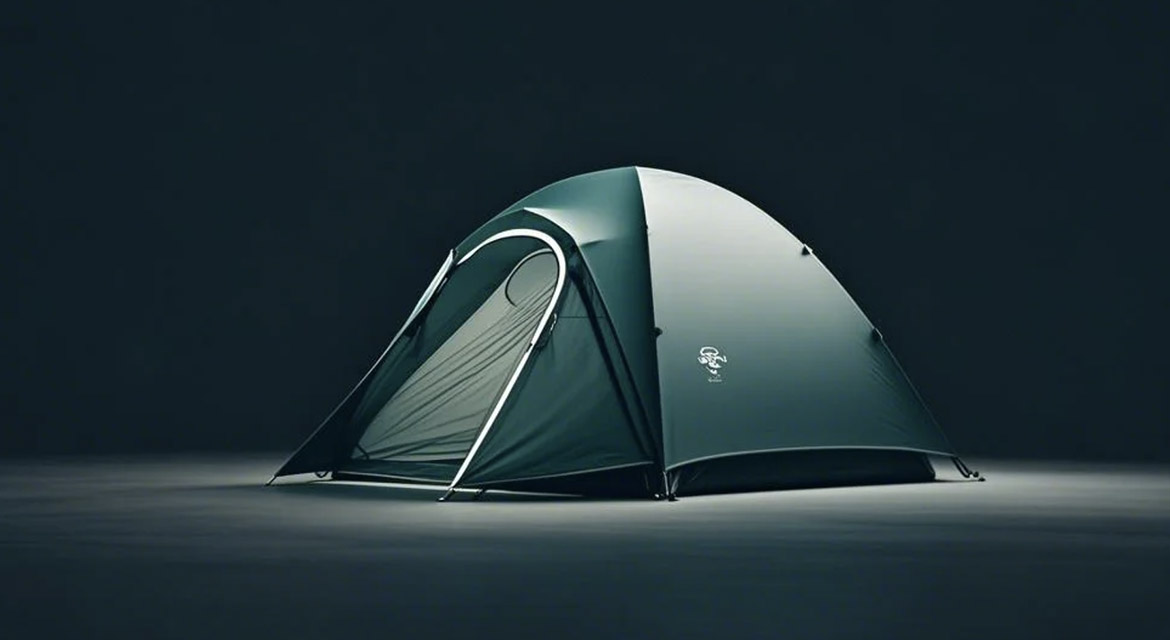
Tents

Type
Backpacking, Family, Inflatable, Military

Material
Ripstop Nylon/Polyester With Silicone Or Pu Coatings For 20d–70d Waterproofing

Printing
Screen Printing, Thermal Transfer, Digital Direct Printing, Etc.

ECO
Recycle Old Tents
- 1. Design and Engineering
- Concept Development: Define the tent type (backpacking, family, inflatable, military), capacity, and use case (camping, events, emergencies).
- Technical Specifications:
- CAD modeling for structural integrity, dimensions, and features (doors, windows, ventilation).
- Design considerations: Weight-to-strength ratio, weather resistance, and ease of setup.
- Prototyping: Build a physical model to test aerodynamics, stability, and user ergonomics.
2. Material Selection- Fabric:
- Canopy/Rainfly: Ripstop nylon/polyester with silicone or PU coatings for waterproofing (measured in denier, e.g., 20D–70D).
- Floor: Heavy-duty PU-coated polyester (150D–300D) for puncture resistance.
- Mesh: Breathable polyester or no-see-um mesh for airflow.
- Poles: Aluminum (7075-T6 alloy) or fiberglass; segmented with shock-corded joints.
- Hardware: Corrosion-resistant zippers (YKK® AquaGuard), steel stakes, reflective guylines, and buckles.
- Sustainability: Recycled fabrics, PFC-free waterproofing, or biodegradable materials.
3. Fabric Cutting and Preparation- Pattern Making: Convert 3D designs into 2D templates for panels (walls, rainfly, floor).
- Cutting:
- Laser or ultrasonic cutting machines ensure precision and reduce waste.
- Pre-treat fabrics with waterproof coatings or laminates.
- Seam Tape Application: Heat-seal waterproof tape to critical seams.
4. Sewing and Assembly- Panel Construction: Sew fabric panels into tent walls, rainfly, and bathtub-style floor (raised edges to block water).
- Zipper and Mesh Integration: Attach zippers to doors/windows and stitch mesh panels for ventilation.
- Reinforcements:
- Bar tacks at stress points (pole sleeves, guyline loops).
- Webbing straps for load distribution.
- Pole Sleeves/Clips: Sew sleeves or attach clips to connect poles to the tent body.
5. Pole Manufacturing- Material Processing: Cut aluminum or fiberglass rods to length; deburr edges.
- Assembly: Join segments with ferrules (metal connectors) and elastic shock cords.
- Bending: Use hydraulic presses to shape poles for dome or tunnel tents.
6. Waterproofing and Seam Sealing- Apply liquid sealant or tape to all stitched seams.
- Test hydrostatic resistance (e.g., 1,500–5,000 mm rating) to ensure no leaks.
7. Quality Control- Durability Testing:
- Wind Resistance: Simulate storms in wind tunnels (e.g., 50+ mph winds).
- Load Testing: Apply weight to poles and seams to mimic snow or debris.
- Field Testing: Real-world trials in extreme conditions (rain, snow, UV exposure).
- Compliance: Meet safety standards (CPAI-84 for flame resistance, REACH for chemicals).
8. Final Assembly- Attach rainfly, guylines, and stake loops.
- Package poles, stakes, and repair kits with the tent.
9. Packaging- Compression: Fold and roll tents into stuff sacks for compact storage.
- Labeling: Include waterproof ratings, capacity, setup instructions, and eco-certifications (e.g., Bluesign®).
- Retail-Ready: Boxed or hung with branding for store displays.
10. Distribution- Ship to outdoor retailers, e-commerce platforms, or disaster-relief organizations.
Key Innovations- Ultralight Materials: Dyneema® Composite Fabric (DCF) for high strength and minimal weight.
- Inflatable Tents: Replace poles with air beams for rapid setup.
- Solar-Ready Designs: Integrated solar panels or ports for charging devices.
Sustainability Focus- Recycled Fabrics: Post-consumer PET bottles transformed into polyester.
- Circular Economy: Take-back programs to recycle old tents.
- Low-Impact Dyes: Water-based inks and dyes to reduce chemical runoff.