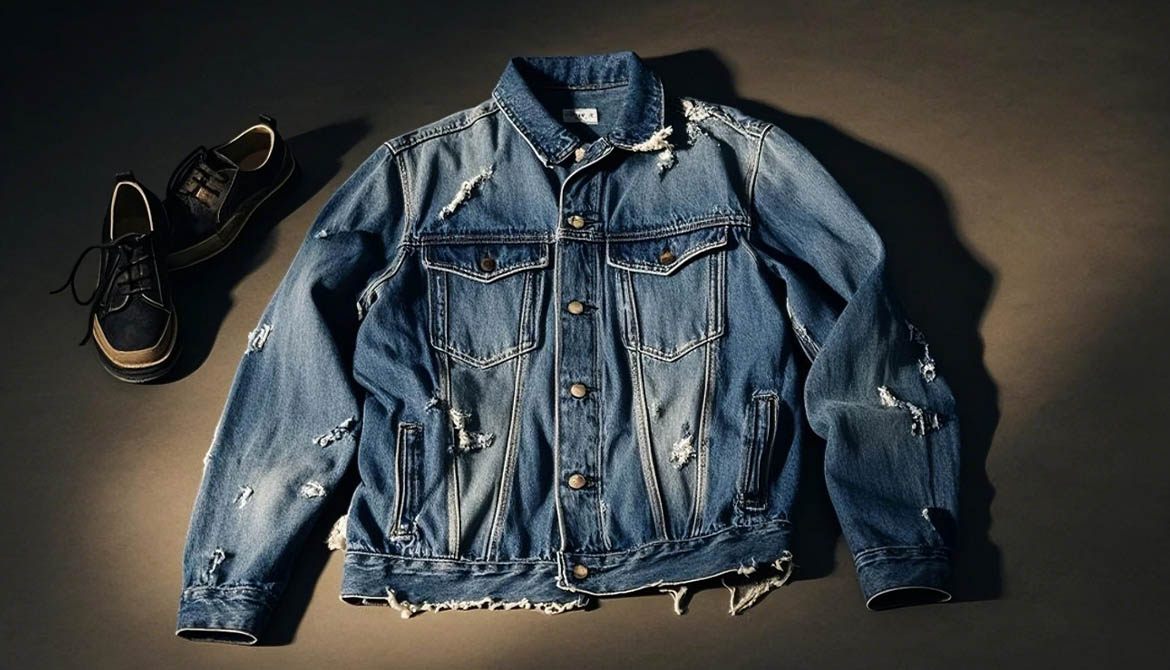
Denim Jacket

Fabric
Lightweight 5-12oz
Mid-Weight 12-16oz

Embroidery
High Density Embroidery Machine

Printing
Screen Printing, Digital Direct Printing, Etc.

Washing
Enzyme & Stone, Acidic , Hydrogen Peroxide,Alkaline.
1. Design and Pattern Making
Design Concept: Designers create sketches or digital renderings of the denim jacket, considering trends, functionality, and target audience.
Pattern Making: Patterns are drafted based on the design. These patterns serve as templates for cutting the fabric into specific shapes and sizes.
Prototyping: A sample jacket is made to test the design, fit, and functionality. Adjustments are made to the pattern if necessary.
2. Fabric Selection and Preparation
Denim Fabric: The primary material is denim, typically made from cotton or a cotton blend. The weight and texture of the denim (e.g., lightweight, mid-weight, or heavy) are chosen based on the jacket’s intended use.
Washing and Treatment: The denim may be pre-washed or treated to achieve specific finishes, such as stone washing, acid washing, or enzyme washing, to create a worn or faded look.
3. Cutting
Laying the Fabric: Denim fabric is spread out in multiple layers on a cutting table.
Cutting the Pieces: Using the patterns, the fabric is cut into individual pieces (e.g., front panels, back panels, sleeves, collars, and pockets) with industrial cutting machines or manually.
4. Sewing and Assembly
Stitching: The cut pieces are sewn together using heavy-duty sewing machines. Key steps include:
Attaching the front and back panels.
Sewing the sleeves and attaching them to the body.
Adding pockets, collars, and plackets.
Reinforcement: Stress points (e.g., seams, buttonholes, and pockets) are reinforced with double stitching or bar tacks for durability.
Hardware Attachment: Buttons, rivets, zippers, and snaps are added during this stage.
5. Washing and Finishing
Washing: The assembled jacket undergoes washing to soften the fabric, remove shrinkage, and achieve the desired look (e.g., distressed, faded, or vintage).
Dyeing (if needed): Additional dyeing may be done to achieve specific colors or effects.
Drying: The jacket is dried using industrial dryers or air-drying methods.
6. Quality Control
Inspection: Each jacket is inspected for defects in stitching, fabric, or hardware.
Fit and Functionality: The jacket is checked for proper fit, alignment of seams, and functionality of zippers, buttons, and pockets.
Trimming: Loose threads are trimmed, and any final adjustments are made.
7. Pressing and Packaging
Pressing: The jacket is pressed using steam irons or industrial presses to remove wrinkles and give it a polished look.
Packaging: The finished jackets are folded, tagged, and packed for shipment. Tags may include size, care instructions, and branding.
8. Distribution
The jackets are shipped to retailers, wholesalers, or directly to customers.